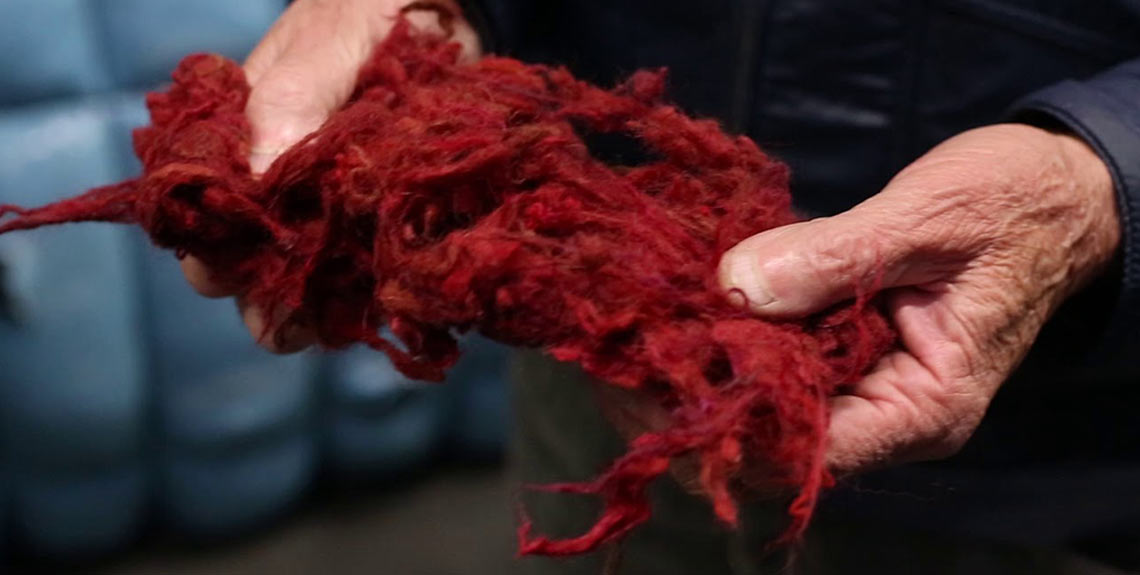
The regenerated wool of Prato

The new life of fabrics. When artisans regenerate manufacture
Over the years, people have become increasingly aware of the issue of sustainability and environmental impact. This led to the revival of ancient tissue regeneration techniques, a process that had its greatest expansion in the Italian city of Prato during the post-war period.

What is regenerated wool?
Like regenerated cotton, regenerated wool is also obtained through the complete recycling of old clothes or scraps from other processes.
These rags undergo a manufacturing process, called the regeneration cycle, in which they are processed in a way as to obtain a completely new fabric which restores the original beauty of the fibers.This process is not something new: it has been known for many years. Regenerated wool is in fact a Prato historical tradition where since the end of the nineteenth century, the “cenciaioli” of the textile district which includes 12 Municipalities and a population of over 300 thousand inhabitants have always sorted rags based on colors and materials, to transform them in wool yarns to weave. It was said that all the rags ended up in Prato and it is precisely from those throw away rags that a new art was born.
In recent years, these fabric recycling processes have largely taken off again, thanks to the interest in the tradition of ancient crafts, and above all thanks to the counscious sensitivity around sustainability and respect for the environment. In fact, creating regenerated wool significantly reduces the environmental impact without removing the original characteristics of softness and purity from the wool.

But how is regenerated wool born?
The first step in obtaining regenerated wool is that of collecting rags and old clothes. Those still usable are resold or donated to humanitarian associations while the others begin their process to become regenerated tissues.
Once the rags to be regenerated have been identified, they are divided both by type of fabric and by color. They are then deprived of all accessories, such as buttons, zippers, linings and labels. Once the fabric is so “cleaned”, its fraying can begin. This process is used to obtain mechanical wool, i.e. fibers that will be refined and spun again, to obtain new fabrics that retain all the characteristics of the original fibers.


The advantages of wearing regenerated wool
Wearing regenerated wool is not only a trendy choice but also of an advantage in terms of sustainability and environmental impact.We think that for the production of a “new” cashmere sweater, up to 6,500 kg of CO2 are released into the atmosphere, unlike a regenerated cashmere sweater that reaches just 100 grams.
Water consumption is also significantly reduced: the production of regenerated wool reduces water consumption by 90%. Not only CO2 and water: the savings from the production of regenerated wool also concern the use of energy, chemicals and dyes. Compared to the production of cashmere sweater with virgin fibers, a regenerated cashmere sweater significantly reduces the environmental impact, saving: 77% of energy, 90% of water, 90% of chemicals, 95% of Co2 and 100% of chemical dyes.
In conclusion, in this way it is possible to save over 22 thousand tons of waste fabric that does not end up in landfills but returns to live a new life.

The Bertola Sisters
They are two sisters who have been running a small knitwear factory in Prato for forty years using Prato yarns made from “regenerated” wool. Their product line is the result of a meticulous collaboration between different professionals who transform the yarns into regenerated winter accessories.
“For a long time, regeneration has been considered a ‘series B’ process compared to the use of pure virgin wool. On the contrary, these quality yarns are historically selected by cenciaioli and skilled craftsmen from Prato and have an added value because they come from the recovery of disused wools, which from waste become new raw materials “. The aunts, specialized in fine knitwear, produce gloves made of 98% of cashmereri generated, the “fine” hat and the “ganzo”, a neck warmer that becomes a hat, made of merino wool (50%) and regenerated cashmere (50%) or regenerated wool (40%), polyamide (22%), silk (20%) and other fibers.
“It is not always easy to find yarns of this kind, so from time to time we work with different fiber compositions, looking for the best combinations. In this way, our supply chain is shortening, moving from third party processing to direct sales to consumers.
